Networking Noodles
1 May 2024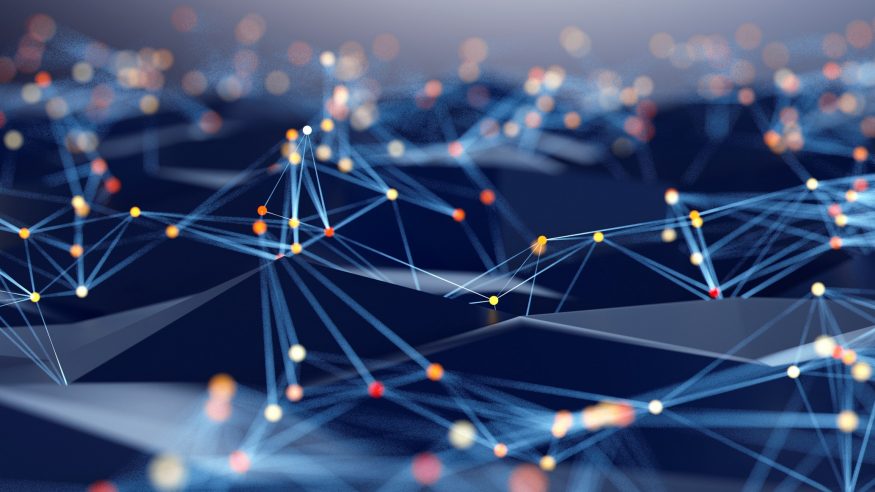
It is fair to say that over the last 18 years I have thought A LOT about lean, and indeed, about a whole plethora of other related improvement methodologies. I’ve read many articles, attended many conferences, read many LinkedIn posts where a variety of #lean men fight about who knows #lean best (*cough* me) and so it is safe to say that its quite difficult to catch my attention with a dazzling new insight on all things lean related.
The last time I had that lean *WOWSERS* feeling was when I encountered Prof. Nicola Burgess’ work when she was at Warwick Business School. She led a team that evaluated a five year partnership between the NHS and the US Based Virginia Mason Institute which was designed to bring about healthcare improvement using their version of the Toyota Production System. Virginia Mason is the lean hospital mothership. Although they are a private healthcare institution (commercial, customer centric transactions can certainly help to focus the productivity mind) they have, for 22 years now, committed to the widescale implementation of a holistic lean approach and they’ve been immensely successful at it. You can read more about them here – What is Virginia Mason Production System | Virginia Mason Institute. Could their approach be used to bring about transformation in 5 English Trusts in the NHS?
Usually, when listening or reading a case study about a lean transformation, I check tick boxes in my mind. Importance of leadership ☑ getting the right metrics ☑ getting middle management onboard ☑ how hard it is to keep the momentum ☑ not everything worked how they hoped ☑, but when I saw an interim results presentation by Nicola about the Evaluation of NHS partnership with Virginia Mason Institute (health.org.uk) I was dazzled by not just the narrative of what had happened, what worked and what didn’t work, I could literally SEE it.
I’ve always loved connecting things, joining the dots. I was obsessed with astrological charts, loving seeing the recognisable dot to dot connections on paper and then in the night sky. My External Engagement role is about identifying opportunities to bring people together, weave connections and build relationships. The intellectual contribution to lean which I am most proud of, is in itself a web of connected concepts and methodologies. I believe that that’s what’s important about amazing organisations – that they think about things holistically, that the respective parts of the organisation don’t act in isolation, that they consider their role within the whole and that they collaborate around common goals (hopefully, the customer), that they are full of powerful and productive networks. And here, within this evaluation of how different lean implementations had fared, I could suddenly see how interconnected the organisation actually was around improvement activity. Through a kind of brilliant visual management, created by Emily Rowe, each NHS Trust could be instantly assessed in terms of how the constituent parts connected on improvement matters. And the results were obvious.
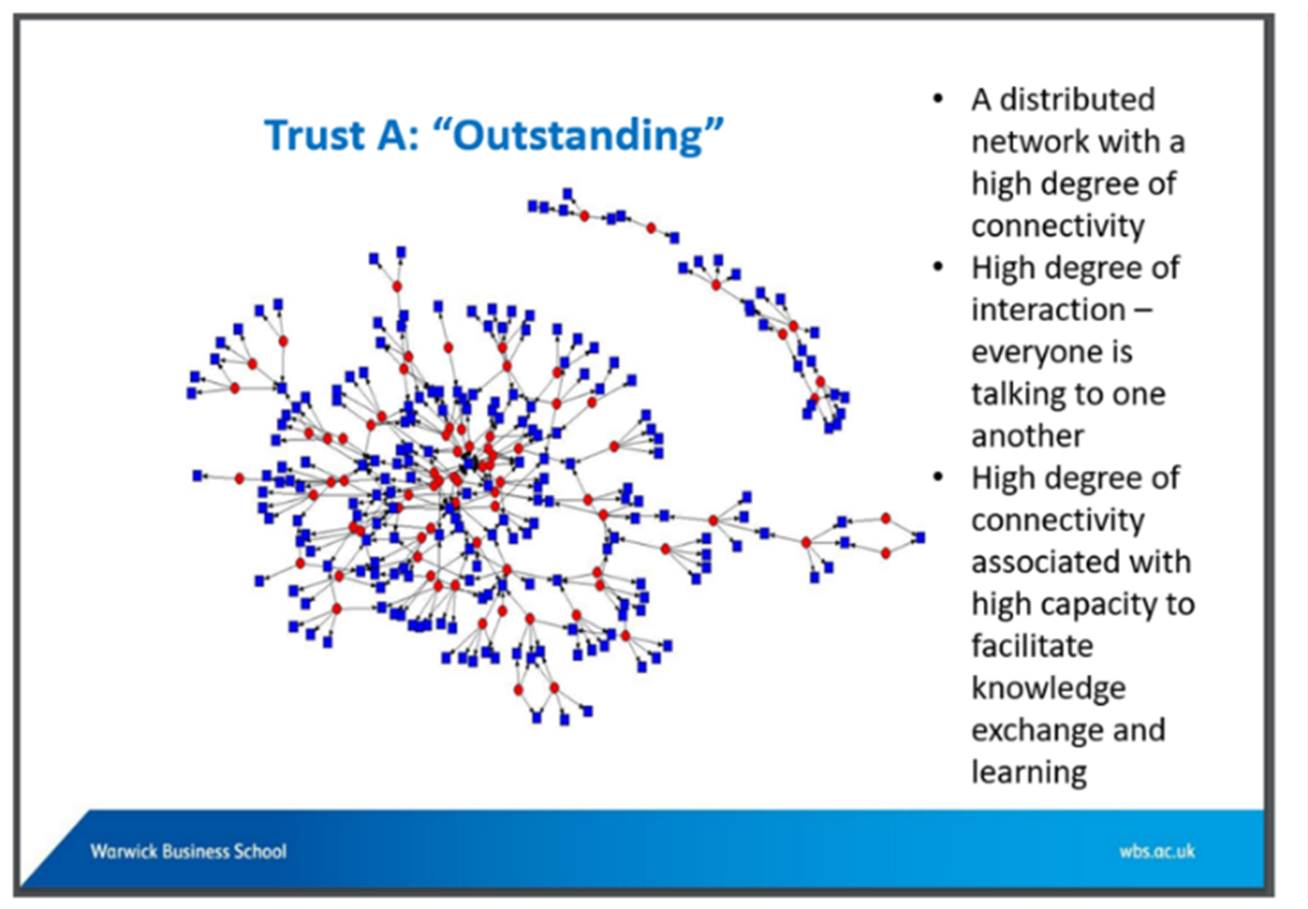
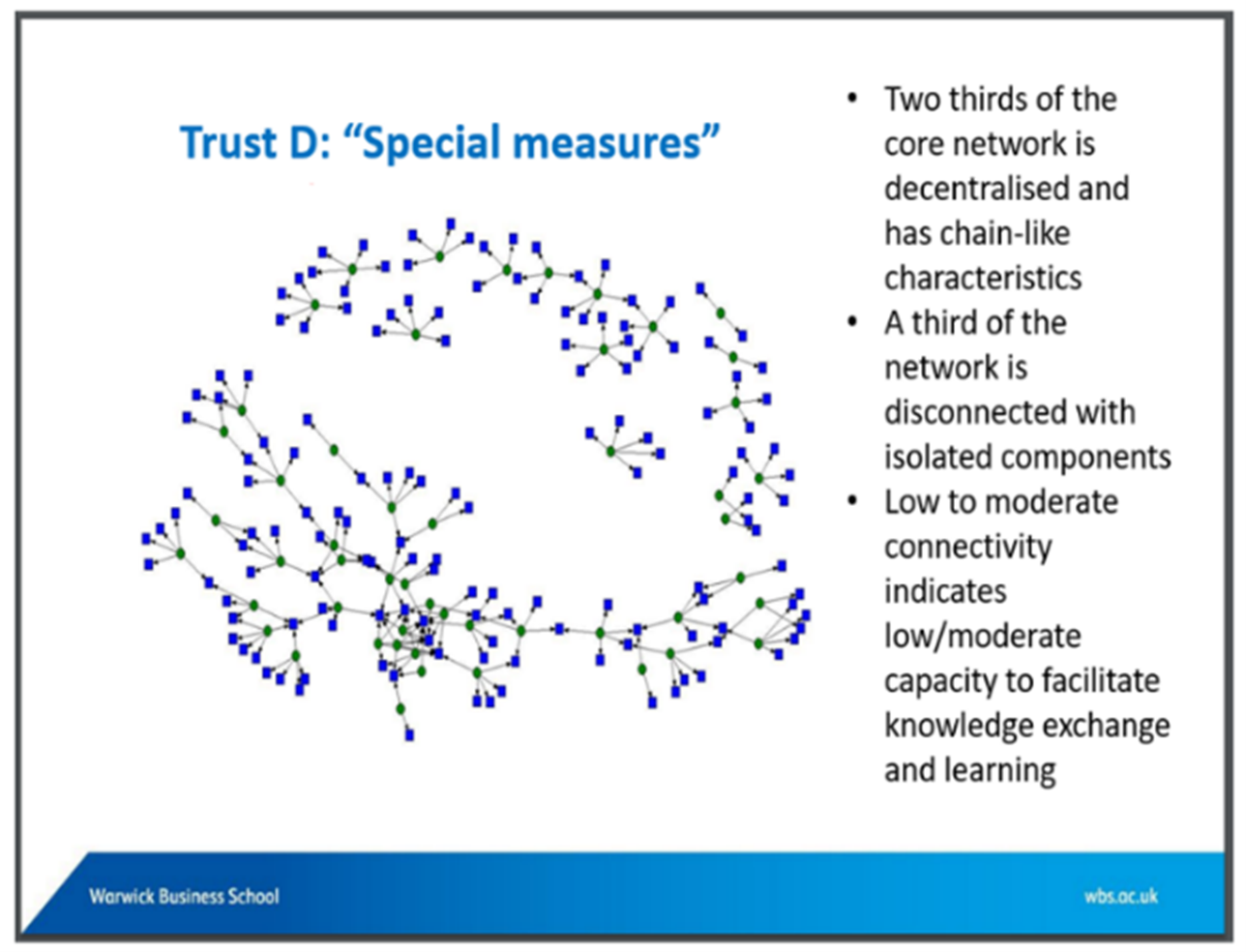
The technique shown is Organisational Social Network Analysis (OSNA) which “is a systematic approach to uncovering and visualising the presence and patterns of relationships, and the flow of information, influence, and collaboration within and across organisational settings”. It was used here to “understand how knowledge about improvement was being mobilised among healthcare professionals within each of the five hospitals that took part in the five-year partnership between the NHS and the US-based Virginia Mason Institute (VMI). (Burgess and Rowe, 2023). Why social networks are vital for continuous improvement | News | Warwick Business School (wbs.ac.uk)
There’s obviously lots to this research methodology, if it intrigues you, you can read more about it here Improving Company Performance with Organizational Network Analysis and there’s also the International Network for Social Network Analysis | INSNA as a collective body of OSNA enthusiasts, but to summarise what is happening within this research, the spiderwebs illustrate how people are talking / working / collaborating around particular issues. I don’t really understand how the lines are created and the specifics of what they represent, rather, I just understand that they represent that a connection exists. But yes, it’s wonderful to be able to see the circulatory and nervous system of the inner workings of an organisation in this way (as if the organisation, as an organ, had spent some time in a vat of some kind of acid, exposing the biological highways and networks that make the organ live and breathe – perhaps I go too far 😁).
Improvement is a great thing to examine using this approach because, as (I have mentioned many times previously🙃) the key to organisational improvement is learning. Embracing structured organisational learning, at every level, at every scale, delivers dynamism, innovation, and, when channelled in the right direction, success. And what is learning if not the sharing of knowledge through discussion, connecting with people across organisational boundaries to achieve collaborative goals?
It makes absolute sense to me to explore organisational effectiveness and efficiency by exploring employee connections in this way. How are we connecting with each other as an organisation? Can we see patterns? Are we able to work together to achieve common goals?
I need to learn more about it, but I’ve started following Jeppe Vilstrup Hansgaard on LinkedIn because he seems to be an expert in this area too but yes, I love this way of looking at organisations in terms of the thousands of connections that occur and thinking about whether these connections are aligned and effective. Networks are everything, we know this, so let’s visualise them.
Once you have clarity on the way things actually are, a current state, then you can develop a road map to do something about what you have found. You can create a new future.
- McMullin’s Tandem of Co-Production
- The Joy of John Parry-Jones
- The Perils of Disappointment
- The Shield of Shame
- Customer Care and Organisation Innovation
- Hooray for Humanity!
- Angry Lemons
- Double Meanings
- Ticketing Masterplans
- When will it all end …
- Lifetime Loyalty and Taylor Swift
- Looking at Things Differently
- Networking Noodles
- Addicted to Truth
- Designs on Service Design
- The Multiple Joys of Universal Design
- Hungry Cultures
- Event Lean
- The Traffic Analogy
- Moving on Up
- Rosé Cava Revolution?
- Powerpoint Sneaky Lean
- Writing about Writing
- ChatGPT Response: Exploring the Art of Expression: Unveiling the Magic of Writing in the Style of Sarah Lethbridge
- Help to Grow Coldplay Style
- Caring IS Everything!
- Institutional Flapping
- “Just Do the Next Right Thing”
- Trust Thermoclines
- Organisational Tempo
- The Inaugural Lethbridge Customer Service Awards
- Vaccine Lean – The Dawn of the Water Spider
- The Queen and Lean
- Decisions, Decisions, Decisions
- Peaceful Protest
- Tesla Tales
- Back to Reality!
- Carrots, Sticks and Buckets of Time Tricks
- The Great Pandemic Pause
- Organisational Therapy
- April 2025 (1)
- March 2025 (2)
- February 2025 (1)
- January 2025 (1)
- December 2024 (1)
- November 2024 (1)
- October 2024 (1)
- September 2024 (1)
- July 2024 (2)
- June 2024 (1)
- May 2024 (1)
- March 2024 (1)
- February 2024 (2)
- December 2023 (2)
- October 2023 (2)
- September 2023 (1)
- July 2023 (3)
- June 2023 (1)
- May 2023 (1)
- April 2023 (1)
- March 2023 (1)
- February 2023 (1)
- January 2023 (1)
- November 2022 (1)
- October 2022 (2)
- August 2022 (2)
- July 2022 (1)
- May 2022 (2)
- April 2022 (1)
- February 2022 (1)
- January 2022 (1)
- December 2021 (2)
- November 2021 (1)
- October 2021 (1)
- September 2021 (1)
- August 2021 (1)
- July 2021 (1)
- May 2021 (2)
- April 2021 (1)
- March 2021 (1)
- January 2021 (1)
- December 2020 (1)
- October 2020 (3)
- August 2020 (1)
- June 2020 (2)
- April 2020 (1)
- March 2020 (1)
- February 2020 (1)
- December 2019 (2)
- October 2019 (1)
- September 2019 (1)
- August 2019 (1)
- July 2019 (1)
- June 2019 (1)
- February 2019 (3)
- October 2018 (1)
- September 2018 (1)
- March 2018 (10)
- April 2016 (1)
- January 2015 (3)
- July 2014 (9)
- September 2013 (1)