5 Counter Intuitive Elements of Lean
26 April 2020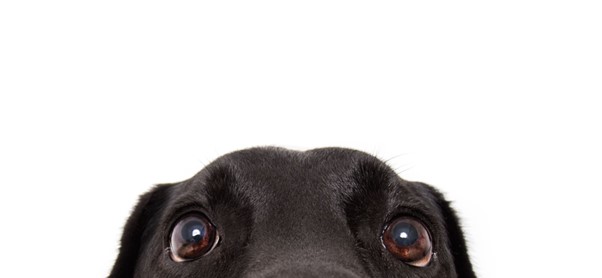
(or Lean is Weird)
Relatively early in the lockdown, when the usually ever-bountiful supermarkets were ransacked by worried shoppers, leaving aisle upon aisle of bare shelves, criticisms of lean began to materialise. ‘Just-in-time is to blame’, ‘supermarkets don’t hold any stock anymore so they can save money’, ‘supplies are delivered ‘little and often’, the inference being that such practices leave us very vulnerable to shocks and times of crisis.
Which is absolutely correct. What a lean thinker would ask people to think about is ‘how feasible is it to always hold as much food as we need to survive a global pandemic triggered lockdown?’ and ‘how much waste would be there be every week?’ It’s not as if supermarkets had cracked ‘zero waste’ before the Covid-19 crisis happened anyway. Plus, they are under an amazing amount of pressure to deliver ‘value for money’ for customers so it is only natural that they will pursue practices that aim to reduce cost and minimising stock levels, where levels are aligned to demand, to achieve this.
Lean is full of ideals that can manifest themselves imperfectly within a range of different scenarios. When the usual ‘once every 3 years’ purchase of plain flour is suddenly, and without warning, quickly replaced by ‘it’ll use up an hour or two and I always fancied giving it a go’ bread baking aspirations of the masses – it’s far too much for lean to deal with. Most supermarkets work on supply chain replenishment principles as described, borne from the fourth lean principle, that of ‘PULL’.
Pull asks lean organisations to make what has only been bought or ordered. If this was perfectly achieved it would produce a zero waste environment, but when it comes to all of the many different products that supermarkets stock, basing everything on pull simply wouldn’t be practical. How could you cope with the demand for barbecue food on a sunny weekend if you were relying on stocking levels based on the rainy weekend previous? With or without a global pandemic. So, the truth is that no lean principle can ever be completely achieved.
Indeed, some lean principles should be actively fought against in order to make organisational sense. The best example I can think of here is the lean ideal of ‘one piece flow’ which asks us to focus on making things one at a time as this ensures the shortest possible lead time for the delivery of that one product, zero waste and the best chance for complete quality. However, what does this mean for making cornflakes for example? For making aspirin? Making one box of aspirin, one box of cornflakes at a time? It would make no economic sense because economies of scale are real. I have written more on this here.
So lean is a funny thing – it can never be purely achieved and sometimes needs to be overridden. It’s often called ‘common sense’, yet there are lots of counterintuitive elements and things that need to be ‘uncovered’ or ‘taught’. Over the years, I’ve developed a list of the ones that interest me the most and I thought I’d share them with you now, to give an insight into lean’s strangeness. So whilst we’ve been discussing it, let’s start with Pull …
Lean Counterintuitives
1. Pull or right to left thinking
In order to improve, lean asks us to think about everything that is happening as we track backwards from purchase. Humans go forward. They start at the beginning and move towards the end. That’s just what we do, how we live each day, each year of our lives. Lean asks us to think about what needs to be achieved and work backwards from that point to achieve it, reducing the amount of time it takes to do so. This does not come naturally to us AT ALL. Time stretches out before us usually. Looking backwards is uncomfortable and we resist, yet how powerful a mechanism of investigation it is in order to move forward more positively as it helps us to focus on the things that are truly important.
2. To get quicker at doing things, you have to become obsessed with quality
Working faster often means that you might lose some of the quality of what you do, a clumsily written sentence, a poorly cut hem and so when we talk about lean being a methodology that looks to reduce end to end lead times, it would be easy to think that we are prepared to do so at the expense of quality. That we were happy with shortcuts. The reverse is true however. The ONLY way that you can become faster is to become obsessed with quality. Indeed, the ‘andon’ concept of calling for help, even sometimes stopping the line, in order to problem solve and put failsafe prevention mechanisms in place, can be said to be slowing things down so as to ultimately, get faster. So yes, to get quicker, you need to slow down and think about the quality of your work. If you produce poor quality, you’ll lose your customers
In a similar vein, sometimes to become quicker at delivering products or services to customers, you need to increase the amount of work that operators do leading us to ….
3. Reducing lead times might mean that workers have to do more work
There’s a kind of misnomer out there that lean is all ‘cut, cut, cut’ when actually, sometimes we ask employees to do MORE to deliver a better service to customers. I talk about my 12 week maternity scan to explain this. After checking into reception I saw 4 different people. 1 to check my urine, 1 to weigh me, 1 to scan me and 1 consultant. The whole process took 2 and a half hours to complete as I queued for each part of the process. As I sat patiently to move to each stage in the waiting room, I could see a variety of medical staff looking for patients, looking for files. What would have been a better experience for me, and one that was ultimately more efficient, would be for the scanning team to scan me and also check my urine, note down my weight at the same time. Better for me, but more work for those individuals. The same principle can be applied in many different work scenarios, if the worker takes on a little bit more, the customer will often have a better experience. The problem is though that…
4. Humans like batching not ‘one piece flow’
We prefer focusing on one task and doing it over and over again. ‘I’m doing urine tests this morning’… ‘I’ll let all of these registration forms collect for a while and I’ll blitz them all one Friday afternoon’. This is because we feel more comfortable once in the rhythm of task than chopping and changing our head and our hands to do different things. The truth is that it is quicker FOR US to work in a batch, we get faster and faster as we click into the groove, but we forget about the poor customer who is waiting those 2 weeks until we manage to get into our ‘I must blitz inputting those registration forms’ mindset.
5. The more inventory there is, the longer the lead time
Something that I still get my head twizzled about is the fact that the more inventory or stock that exists in the system, the longer the lead time experience for every product or service within that system. To bring us back to the beginning of the article, if you have a supermarket system that is full enough to deal with a global pandemic, food will have been loitering waiting to be used within that system for a very long time – not a great idea when food is perishable!
So yes, lean can be weird because there are many conditions and ‘yes buts’ and ‘if this then this but if that then the other’.. that’s why understanding that lean primarily is about delighting customers, reducing lead time and/or maximising value and a scientific approach to work is essential.

Once you’ve grasped those three overriding principles, you can then start thinking and understanding all of the myriad of concepts that comprise the application of lean (one piece flow, standard work, just in time etc. etc.) which you will inevitably have to adapt. Most crucially, as long as you reflect, experiment and learn à la PDCA, you will always be on the path of improvement, so lean will always be win win.
Comments
8 comments
Comments are closed.
- Customer Care and Organisation Innovation
- Hooray for Humanity!
- Angry Lemons
- Double Meanings
- Ticketing Masterplans
- When will it all end …
- Lifetime Loyalty and Taylor Swift
- Looking at Things Differently
- Networking Noodles
- Addicted to Truth
- Designs on Service Design
- The Multiple Joys of Universal Design
- Hungry Cultures
- Event Lean
- The Traffic Analogy
- Moving on Up
- Rosé Cava Revolution?
- Powerpoint Sneaky Lean
- Writing about Writing
- ChatGPT Response: Exploring the Art of Expression: Unveiling the Magic of Writing in the Style of Sarah Lethbridge
- Help to Grow Coldplay Style
- Caring IS Everything!
- Institutional Flapping
- “Just Do the Next Right Thing”
- Trust Thermoclines
- Organisational Tempo
- The Inaugural Lethbridge Customer Service Awards
- Vaccine Lean – The Dawn of the Water Spider
- The Queen and Lean
- Decisions, Decisions, Decisions
- Peaceful Protest
- Tesla Tales
- Back to Reality!
- Carrots, Sticks and Buckets of Time Tricks
- The Great Pandemic Pause
- Organisational Therapy
- Late Night Wordleing
- Vaccine Lean
- Chief Letters of Complaint Officer
- AMBAZING Accreditation!
- January 2025 (1)
- December 2024 (1)
- November 2024 (1)
- October 2024 (1)
- September 2024 (1)
- July 2024 (2)
- June 2024 (1)
- May 2024 (1)
- March 2024 (1)
- February 2024 (2)
- December 2023 (2)
- October 2023 (2)
- September 2023 (1)
- July 2023 (3)
- June 2023 (1)
- May 2023 (1)
- April 2023 (1)
- March 2023 (1)
- February 2023 (1)
- January 2023 (1)
- November 2022 (1)
- October 2022 (2)
- August 2022 (2)
- July 2022 (1)
- May 2022 (2)
- April 2022 (1)
- February 2022 (1)
- January 2022 (1)
- December 2021 (2)
- November 2021 (1)
- October 2021 (1)
- September 2021 (1)
- August 2021 (1)
- July 2021 (1)
- May 2021 (2)
- April 2021 (1)
- March 2021 (1)
- January 2021 (1)
- December 2020 (1)
- October 2020 (3)
- August 2020 (1)
- June 2020 (2)
- April 2020 (1)
- March 2020 (1)
- February 2020 (1)
- December 2019 (2)
- October 2019 (1)
- September 2019 (1)
- August 2019 (1)
- July 2019 (1)
- June 2019 (1)
- February 2019 (3)
- October 2018 (1)
- September 2018 (1)
- March 2018 (10)
- April 2016 (1)
- January 2015 (3)
- July 2014 (9)
- September 2013 (1)
Brilliant Sarah and beautifully written
Aw thanks John! X
Very well written article. Good reflections. Thanks.
Thank you – I found this really interesting. Lean fascinates me!!
Nice list of counter-intuitive technical aspects of Lean. Another one, at least as Toyota practices Lean, is that there is not one final destination, but more of a never-ending process of learning, improvement and adaptation. Our brain does not love that. Interestingly, though, it dovetails well with the dynamic and unpredictable conditions that constitute life … better than trying to “implement” apparent ready solutions. It does demand that a team practice *how* to develop solutions in a scientific-thinking way – a useful meta skill for any human!
Along these lines, here’s one possible definition of Lean: “Lean = the permanent struggle to flow value to one customer.” (https://www.slideshare.net/mike734/a-definition-of-lean)
Thanks Mike! I love that – Lean is definitely a permanent struggle alright! Thanks for sharing 🙂
Nicely written Sarah. Regarding point 4, it’s not that humans love doing one thing over and over, and it’s also not faster. Humans love flow and have been conditioned to not have control from beginning to end. Give someone a clear pathway from start to finish, and the flow state matches or exceeds any derived pleasure that is assumed in doing one single thing repetitively. Batching is definitely not faster – try putting 10 envelopes together and you’ll see that one piece wins hands down.
I love that point about how we have been conditioned, and yes, I suppose educated, to focus on one thing at a time. Ahhh the envelope game, I know it well! Have you played the Penny game? This nicely illustrates the ‘waste swopping’ that occurs as an employee moves from batching and undertaking repetitive tasks over and over again to undertaking different elements of roles to reduce lead time. Sure every process is different, but I stand by my point that humans get into a groove of doing one task over and over again – it is quicker. More potential for errors in the end to end system granted. Why repetitive batch tasks is how Henry Ford built his production system, the founding father of the TPS, breaking a task down and someone becoming an expert in that one action.