Thinner Electrical Steels Are Coming Sooner Than You Think – Alexander Washbourne
28 April 2021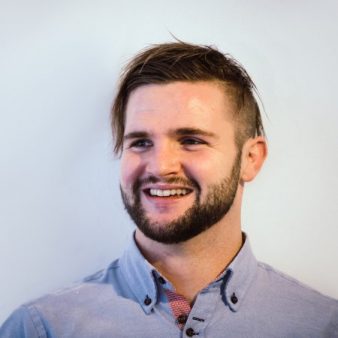
A glimpse of the WMM’20 [Online] 9th International Conference on Magnetism and Metallurgy, November 3rd – 5th, 2020
As an EngD student of Cardiff University’s MAGMA Research Group I was fortunate to receive conference funding from M2A Doctorial Academy to attend the International Conference on Magnetism and Metallurgy. This is an excellent communication forum for experts from industry and research institutes in the area of Soft Magnetic Materials (SMM) to exchange ideas and discuss the advancements in SMMs and their applications in advanced electrical machines. These advancements may very well end up in the electric motors we find within electric vehicles we see on the road the not too distant future. Though there were many interesting speakers and presentations at this year’s conference I would like to use my first MAGMA blog post to draw attention to a topic I am particularly interested in—how a seemingly small reduction in the sheet thickness can significantly improve the magnetic performance of the NOES products. The two papers which covered this topic in depth are shown below and may be found in the WMM2020 conference proceedings which is due to be published very soon.
Electrical Steel and Motors performances, Role of Lamination Thickness
Authors: Mircea Popescu, Nicolas Riviere
Low thickness NGO FeSi electrical steel for high frequency automotive applications
Author: Fiona Robinson
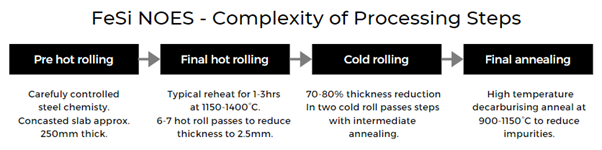
Manufacturing Thinner Electrical Steel Sheets
To begin it is worth noting the relative complexity of manufacturing of NOES steel laminations, Figure 1 shows the additional steel making processes which are applied after the standard mild steel production route to develop the microstructure and texture to achieve the specified mechanical and magnetic properties as well as reduce the steel to the desired lamination thickness.
Reliably manufacturing thinner NOES laminations is no easy feat, it has long been known that thinner materials are much more difficult to process as they are prone to damage due to their relatively high brittleness. This point is best demonstrated by manufacturers needing to improve their lamination stamping process productivity by 35% to make thinner NO20 (0.20mm) products economically viable to manufacture at scale when compared to the thicker NO27 (0.27mm) products just to balance the extra production cost due to the relatively high brittleness. Despite this difficulty, improvements have mainly been realised due to steel manufacturers developing their thermomechanical and composition control processes which have increased the mechanical strength of NOES thereby allowing thin NOES sheets to be handled, processed and operate at high frequencies without failure or fatigue issues.
Up to 25% Material Efficiency Improvement
F. Robinson’s conference paper, summarises recent improvements of thickness reduction on motor weight reduction and energy loss, highlighting the exceptional effort from the electrical steel manufacturing community. Specifically, the paper discusses how a thickness reduction from 0.35mm to 0.10mm permits higher frequency operation which leads to a mass reduction and magnetic material efficiency improvement of up to 25% for the final motor. Overall if you are interested in how the steel manufacturing community are doing their part to increase the power density of advanced electric motors, I highly recommend F. Robinson’s review of recent developments of manufacturing thin and ultra-thin NOES lamination sheets: Low thickness NGO FeSi electrical steel for high frequency automotive applications.
Preliminary Motor Design and Thinner Electrical Steel Sheets
Next we will look at M. Popescu’s conference preceding which walks through a preliminary design process for a high-speed induction motor application. Showing how Motor design limited’s FEM software leverages advances in computational modelling and magnetic measurement capability to evaluate the thermal, mechanical and electromagnetic design limitations early in the prototype design stage for an advanced electric motor. This conference paper was particularly interesting because they demonstrate how FEM results can be integrated with lab-based material characterisation measurements for a range of sample thicknesses to evaluate final motor performance over a range of operating conditions.
Within the paper, FEM generated performance maps for a range of NOES lamination material thicknesses used in the stator and rotor of an induction motor are shown to demonstrate the material selection capability of the FEM software. It was remarkable to see the performance difference in the case of 0.35mm and 0.2mm thick samples where a seemingly small 0.15mm difference was significant enough to affect overall motor performance, suggesting the use of thinner steel laminations are the preferred choice for long-distance high-speed motor applications.
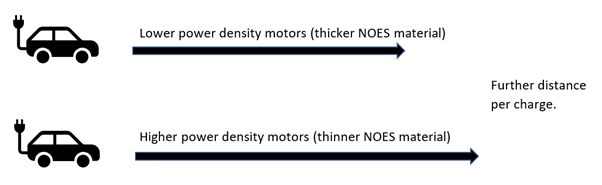
Managing the Trade-offs of Material Selection
At first glance the FEM based results show that the thinner 0.20mm laminations are the better choice in terms of performance for all applications. But considering that thinner materials generally cost more to manufacture and handle, the cost/performance ratio for the 0.35mm may be the better choice for most applications. The thinnest sample (0.20mm) was shown to be more suitable for high torque, higher average speed applications suggesting the more expensive material may justify the extra cost if the application is expected to return more economic value. For example, a large electric lorry which transports heavy goods over long distances may have more economic justification for thinner lamination materials than a small electric taxi which is likely to stop and start a lot, reducing the average speed requirement. Moreover, the perception of cost may change if we consider how improving one component may reduce the demands on other system components. Such as the case when considering the impact of electric motor improvements on the battery pack demands, Figure 2 shows how weight reduction and energy efficiency improvements due to using thinner NOES laminations may increase the maximum driving range per charge.
Selecting the best material for an application can be tricky, especially if the material is a subcomponent within an integrated system of components which have demanding challenges of their own. Nevertheless, using bespoke magnetic measurements and FEM simulations can only help application engineers make design decisions to speed up prototype design cycles. If you are interested in learning more about the preliminary motor design process, I highly recommend looking at M. Popescu’s conference preceding paper which discusses this design method in much more depth: Electrical Steel and Motors performances, Role of Lamination Thickness.
Concluding Remarks
In this article we have reviewed how steel manufacturers and motor design engineers are developing their systems to create increased efficiency, reduced weight high speed rotating machines. This change has been mostly driven by steel manufacturer’s increased ability to produce higher strength thinner lamination materials which are less likely to break during packaging and motor assembly and will help transition rotating electrical machines towards designs which target high speed/high frequency operation. We also discussed how modern FEM software paired with bespoke lab-based measurements may be used to evaluate material motor performance of electrical steels, highlighting how a seemingly small thickness reduction of just 0.15mm is significant to operational performance and efficiency. All in all, I hope this article has given an insight into the trajectory of cutting-edge development within the electrical steel community and shown how important reducing thickness is to the future of rotating electrical machines, machines which may very well end up within the electric vehicles we drive in the future.
Thanks once again to my doctorial academy, M2A for providing funding. Moving forward into my EngD this idea of lamination thickness reduction will be demonstrated as I aim to use MAGMA’s measurement systems and high-performance computers to measure and simulate the effect of high frequency harmonics on magnetic materials for a range of material grades and thicknesses. If you have any questions about this article or what measurement capability and expertise is available within MAGMA research group or just want to connect feel free to reach out to me on LinkedIn or through the MAGMA project. Contact details can be found on the MAGMA website.
Until next time,
Alexander Washbourne
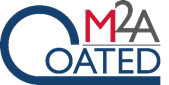