Bags of Airline Innovation
10 September 2020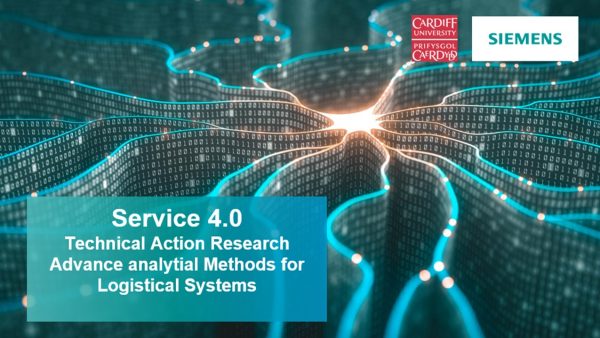
It’s the bane of the air traveller’s life: standing by the carousel, waiting in vain for a suitcase to arrive. Innovators at Siemens Logistics and Cardiff University have developed solutions avoiding unexpected system downtime. Here, the outline of the research project.
“The project began in a fairly usual way during a weekly enhancement workshop at two major Hub airports. Stakeholders, including airport operations and maintenance, baggage handling system suppliers and asset managers, were discussing operational problems. Every baggage handling system is uniquely based on the space that is available in the baggage hall. Depending on the conveyor technology used, the assets causing downtime can vary. In many baggage handling systems, the high-speed terminal transfer tunnel is the part of the system that most critical. The carts or vehicles that run on the tracks are called Destination Coded Vehicles, or DCVs. These need to be in good condition to avoid breakdowns in the transfer tunnel, which cause significant disruption. Every multi–terminal airport operates high–speed transfer lines, and they are up to 3 km long. Passenger transfer time is of the essence, and so DCV systems are capable of transporting bag with 10 m/s (36 km/h).
There are two types of DCV systems that are commonly used. One is of similar design to a roller coaster where vehicles run on tracks. The second type of DCV is based on trays running on conveyors. In both systems the fast–moving transport carrier, especially wheels or bearings are the parts that deteriorate and when fail, causing transfer line shutdowns.
We realised in the workshop that a run-to-break maintenance system was not the best way to assess the status of the DCV carts wearing parts.
The research team came up with an idea to use accelerometers mounted on tracks to capture high vibration transmitted by deteriorated wheels. Additionally, machine vision using modern IoT cameras was applied.
Both vibration or vision data were pre-processed using edge and cloud computing. The Operations and Maintenance teams got a modern dashboard enabling them to service the carts with wheels in the worst condition first.
High values of vibration data reflected when maintenance was pending, the low readings represented carts that had been recently overhauled. This confirmed a correlation between the vibration values and the condition of the vehicle wheels.
The same approach was taken on the system where machine vision was used to identify the condition of guide rollers. Carts with guide wheels which had reached a critical circumference were assigned for maintenance always based on condition. That means the carts with the lowest wheel circumference were assigned for overhaul first.
Solving the biggest problem in an airports’ baggage handling systems has raised attention in both academia and industry. The solutions have to lead to a solution portfolio that enables baggage handling operations to apply modern predictive analytics methods and perform maintenance based on asset condition.
The key here is digitalisation, and with the relevant data captured, O&M organisations get the benefit of significantly reduced system downtime.
Within the research project, entire baggage handling systems got digitalised. Assets got prioritised into highly critical, critical and ‘rest of plant’. Typical highly critical assets are DCV transfer lines or sorters. In general, critical assets are baggage reclaim carousels, oversize baggage hoists, diverters and stackers, just to name a few. For the ‘rest of plant’, are the large number of ‘relatively’ simple straight conveyors. For these, a solution was developed that used data from existing decentralised motor starters for analytical purposes.
The research continues with a new technology called decentralised edge analytics This solution allows successive implementations of condition monitoring technologies in baggage handling systems which consist of tens of thousands of assets.
The condition monitoring solutions have been developed in cooperation between academia and the industry.
We’re excited to think our pioneering process is set to continue to other sectors where goods are transported on moving tracks or conveyor systems.
The cutting edge research on Operational Excellence and Industry 4.0 between Siemens Logistics and Cardiff Business School had laid the foundation for a long-term collaborative relationship.
In future, our plan is to recruit more MSC and PhD students from the Business School and the School of Engineering to work with Siemens Logistics on live projects. These are linked to the use of machine learning, artificial intelligence, and ‘big data’ analytics for solving operational and maintenance issues.
Professors Pauline Found – FoundP@cardiff.ac.uk; Maneesh Kumar – KumarM8@cardiff.ac.uk
The project is one of six winning partnerships shortlisted for innovation by Cardiff University in 2020. To find out more, visit our Innovation and Impact Awards