Beyond Industry 4.0 – Preparing SME Manufacturing Systems for the Future
13 August 2019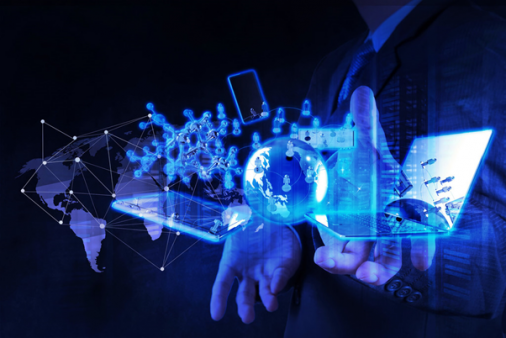
PARC insight by Dr Daniel Eyers, Senior Lecturer Manufacturing Systems Management at Cardiff University
Looking to future proof your business? Good news – you don’t necessarily need to invest in Industry 4.0. In this blog post, written exclusively for PARC, Dr Daniel Eyers emphasizes the importance of getting the fundamentals right, before thinking about the expensive (and potentially unnecessary) manufacturing technologies of Industry 4.0.
Every day my mailbox is bombarded with Industry/Industrie 4.0. Whether it be new government strategies, calls for academic research, hot-off-the press consultancy reports, industry newsletters, or yet-another academic review; Industry 4.0 is everywhere.
Industry 1.0 brought scale to manufacturing, thanks to the generation of steam from coal that powered both production and transportation. Industry 2.0 was a technological revolution, with electricity and telecommunications paving the way for modern production lines. Industry 3.0 represented a digital revolution, with the increasing application of computing in the monitoring, management, and control of manufacturing.
With Industry 4.0 we have the connection of all data and production systems of the entire factory, incorporating a wide range of concepts such cyber-physical systems, cloud computing, and Internet of Things (IoT) –the basic premise is manufacturing excellence, achieved through sophisticated, interconnected, high-tech manufacturing systems.
Interestingly, the only place where I am not consistently bombarded by Industry 4.0 is in my work with manufacturing SMEs. I work with firms from across a wide range of industry sectors, and not one of them has Industry 4.0 on their strategic radar. This is not because they are sleeping through this next industrial revolution – several are extremely attuned – it is just that Industry 4.0 is simply ‘too big’ for them.
I’ll give you an example; when a CAD diagram is already overkill for a welding operator (why not just use a simple sketch?), what actual value would an augmented reality system bring? Because if it doesn’t add value right now, adopting the concepts and technologies of tomorrow’s Industry 4.0 will simply increase costs and threaten profitability today. This is a critical consideration – SMEs typically lack the deep pockets of larger manufacturers and cannot easily absorb the burden of additional investment costs that do not yield at least some short-term benefits.
Revolutions are always difficult, and not everyone survives. Those who do not engage with the revolution may be left behind, as we saw in the demise of cottage textile trades with the industrialization of Industry 1.0 (and subsequently the demise of some of these factories who didn’t quickly adopt electric power in Industry 2.0). But do all companies need to fully embrace the current revolution and the incumbent technologies? And how do we even know which technologies will yield a competitive advantage in Industry 4.0?
For manufacturing SMEs, I think preparedness for the future is often a better strategy than subservient engagement with the latest trend. Because Industry 4.0 will continue to be hugely important to manufacturing, just until Industry 5.0 usurps it. After that we’ll probably see a new noun: just like movies, manufacturing initiatives do not seem to be particularly successful in their sixth instalment.
I can’t predict what technology will underpin the nth manufacturing revolution, but given the previous episodes, my expectation is that it will be based on even more interconnectivity and enhancement for elements of the manufacturing system – and that the best preparedness SMEs can have is to focus on continuous improvement of their manufacturing systems.
Systems matter in manufacturing. Any single given resource may offer an enormous potential for a firm – but unless it can be exploited alongside the other resources in manufacturing, the overall benefits may not be fully utilized. For example, 3D printing is a big part of Industry 4.0. 3D printers supposedly enable enormous flexibility in manufacturing – allowing firms to produce individually customized products to meet individual customer demands. Except they don’t: they are reliant on all other parts of the system (including other technologies and labour), and this in turn constrains their flexibility. The flexibility of the system is therefore very much subject to the flexibility of its component parts, and any part that is particularly inflexible will constrain the whole system.
These findings hold for other manufacturing contexts. A milk-bottling system is only as fast as its slowest component process; bottlenecks exist everywhere. The costs of a laser-etching system will be significantly influenced by the expense incurred from its component processes. Manufacturing systems are an integrated whole: they may have subsystems which interact with the whole system, but the key idea is that the system is organized to optimize some weighted function of its objectives.
I have yet to encounter a manufacturing SME with excellent organization of its manufacturing systems. There have been opportunities to make significant improvements in each firm, the vast majority of which did not necessitate enormous technological leaps. Tools such as the Quick Scan supply chain diagnostic methodology can be enormously helpful in identifying current and future states of the system, from which strategic plans can be developed. Do these plans need to embrace all the principles of Industry 4.0? My experience suggests not.
Some specific technologies such as Cloud Computing, RFID, and aspects of IoT have the potential for realistic systems enhancement in the short term. Other technologies will take much longer to gain significance for SMEs, and some will almost certainly wither before becoming useful. Risk-savvy SMEs will probably not be bleeding-edge adopters in Industry 4.0, or any of the revolutions that follow.
That industry 4.0 is a temporal phenomenon (and something that will eventually pass) is important to remember. Already there are musings over Industry 5.0, even before the current revolution has taken hold. To predict a future beyond Industry 4.0, it helps to remember the past. Whilst leaps in technology have fuelled each of the previous industrial revolutions, in manufacturing the strategic gain has always been in the integration and organization of these changes within the existing systems – initially within the physical confines of individual factories, and subsequently within supply chains and supply networks.
Whatever technology comes next, foundations in effective manufacturing systems organization will be critical, and SMEs should give ongoing focus to these, regardless of their intent to participate in the revolution.
About the Author:

Dr Daniel Eyers is a Lecturer in Manufacturing Systems Management at Cardiff University. His research explores the implications of advanced manufacturing and information technologies for modern Operations Management, particularly in terms of low volume and customized manufacturing.
Recent Publications:
- Delic, M., Eyers, D. and Mikulic, J. 2019. Additive manufacturing: empirical evidence for supply chain integration and performance from the automotive industry. Supply Chain Management: an International Journal (10.1108/SCM-12-2017-0406)
- Eyers, D. and Naim, M. 2019. Project management for effective operations management. In: Wells, P. ed. Contemporary Operations and Logistics: Achieving Excellence in Turbulent Times.. Cham: Palgrave Macmillan, pp. 11-27., (10.1007/978-3-030-14493-7_2)
- Hedenstierna, C.et al. 2019. Economies of collaboration in build-to-model operations. Journal of Operations Management (10.1002/joom.1014)
- Disruptions to Global Supply Chains, Sustainability, and the Inventory Time Bomb
- Sustainability is Driving New Business Dynamics – Repurposing and Connected Collaboration Across Supply Chains
- Digital Technologies – Poison and Medicine for ReMakers
- RemakerSpace reshapes the future
- If they haven’t already, the coronavirus will force companies to re-think their elongated supply chain.