Time to say Adieu to Agile
12 July 2019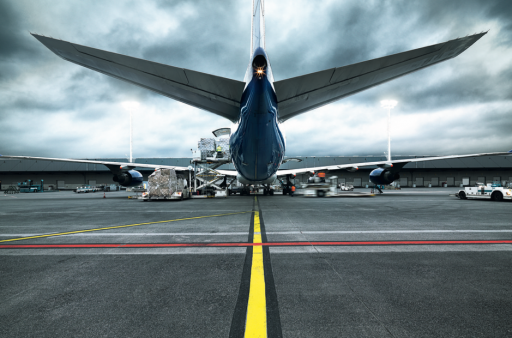
Written by Andy Lahy, Global Head of Logistics Strategy and Innovation at Panalpina.
First of all, our apologies to those of you out there that are strong advocates of Lean, Agile, Six Sigma, Shingo or any other approach that promises to bring continuous improvement or a new culture or transformation to your business.
Please excuse our cynicism, but we´ve seen enough articles on Linkedin about how Lean is a philosophy and not a tool-kit, how Agile promises to improve businesses where Lean has failed, and how Six Sigma, if only it was done correctly and embraced by senior managers, would transform the world.
When it is estimated that 74% of lean programmes are not successful and that the UK alone wasted £37billion on failed Agile projects in one year, isn’t it time that we stopped asking if Lean or Agile is being done correctly, and instead ask if any one of these approaches is right at all?
We call for an end to the debate about the right approach to continuous improvement. Instead, let us seek to understand the fundamentals of how people work together to make things better. It is this understanding that really sits at the heart of any journey towards operational excellence.
Our view is that humans have a natural ability to work together to improve things. In fact, one could argue that working together and improving things is in our DNA. Our world as we know it wouldn´t be here if this weren’t the case, and we are pretty sure it wasn´t all down to Lean or Agile!
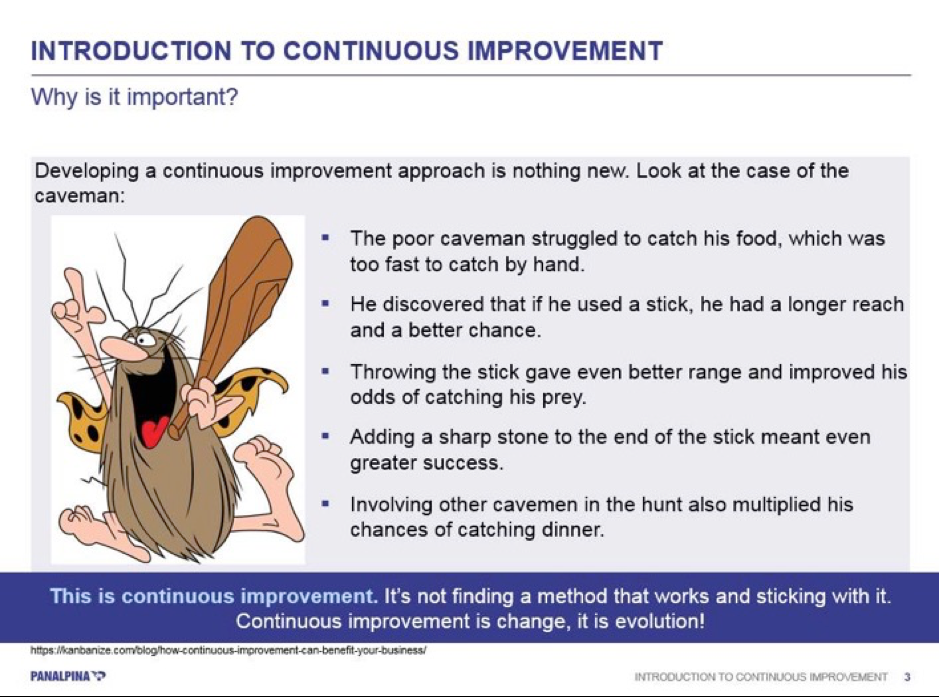
The ideas in this short article are based on research carried out by the Panalpina Centre for Manufacturing and Logistics Research (PARC) at Cardiff University, some of which was recently published in a paper in the Journal of Total Quality Management & Business Excellence, entitled “Towards a theory of operational excellence”.
The core of our argument is that there are more similarities between the many popular approaches such as Lean, Agile, Six Sigma and Shingo, than there are differences, and that any business that blindly sticks to one approach will restrict rather than enable continuous improvement.
Building on the ideas of Dahlgaard and Dahlgaard-Park (1999), operational excellence is about
- developing excellent people, who are able to
- create excellent partnerships with customers, suppliers and wider society, to
- deliver excellent products or services that
- delight customers.
There are clearly multiple ways this can be done. For some, the answer is to look to introduce a “lean approach” or to implement an “agile approach”, or for those that prefer to sit on the fence, the “le-agile approach” is needed. But, in line with the ideas of Professor Mike Wilson, global head of Logistics and Manufacturing at Panalpina, continuous improvement and operational excellence are simply all about winning the hearts and minds of people.
The question to be answered by businesses therefore, is not what is the right continuous improvement approach, but instead, how can we create an approach that enables and engages everyone in the business to want to work together to make improvements?
So, if we advise against using Lean, Agile, Six -Sigma, Shingo or any other off the shelf approaches to do this, what do we recommend exactly to create a culture of continuous improvement?
Simply, we recommend to start by asking yourself what you want to achieve, who the involved people are, both in terms of who will be affected by the change and who will need to work together to make the change. Only when you have this, explore different elements of the existing approaches and select the most appropriate elements from each and bring them together to create an approach that is right for you and the people involved.
This is exactly the approach we used at Panalpina, when we developed our approach to operational excellence. We worked with employees from across the business to take the best from the different approaches, mixed them in with ideas developed by our own team, and created LogEx, an approach that works for us and our customers. Eight years on, LogEx is still going strong and we continue to improve it.
In short, if you want to create a culture of continuous improvement, don´t start by selecting any single approach and blindly try to apply it. Use a pick and mix approach and continuously improve your own continuous improvement approach. To paraphrase Shakespeare’s Juliet, an improvement approach by any name, will work just as well.
- Disruptions to Global Supply Chains, Sustainability, and the Inventory Time Bomb
- Sustainability is Driving New Business Dynamics – Repurposing and Connected Collaboration Across Supply Chains
- Digital Technologies – Poison and Medicine for ReMakers
- RemakerSpace reshapes the future
- If they haven’t already, the coronavirus will force companies to re-think their elongated supply chain.