Logistics Excellence – Applying lean principles to supply chain
7 January 2019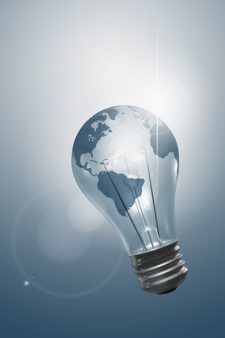
INTERVIEW: Maria Pia Caraccia, Head of Logistics Business Improvement at Panalpina.
Finding the Value in your Supply Chain
Maria Pia Caraccia is a Corporate Business Improvement Manager at Panalpina. She is an expert in global business improvement and has spent the last 6 years developing the Logistics Excellence (or LogEx) programme at Panalpina. In this short interview, she gives us her thoughts on the value of applying lean tools to complex, global supply chains, particularly value stream mapping.
Hi Pia. Thanks so much for taking the time to answer our questions. To get started, could you explain why you first started to focus on lean supply chains?
Hi and thanks for inviting me! I have a background in process improvement and logistics, and if you want to improve how we do things then it’s only a matter of time before you start applying lean principles. Lean is about cutting waste out of your processes, whatever those processes are, and whilst it stems from manufacturing, lean can be applied to a wide range of different activities including logistics. Lean provides us with a huge toolkit of different activities that are tailored to making improvements and reducing waste. The activity that most captured my attention was value stream mapping.
What is value stream mapping?
Value stream mapping (VSM) is a process that allows us a high level view of the entire supply chain. We can use it to visualise waste throughout the supply chain and then remove that waste by applying other lean tools such as kaizen. I’ll come back to this in more detail later, but VSM is unique because it enables oversight of the entire flow of both physical goods and information in the supply chain.
Why do you like it?
I really like VSM because it gives us a different perspective from the standard 3rd party logistics (3PL) approach – traditionally, 3PLs are used to working in the warehouse or with transportation. It’s only recently that we have started to work together with our customers on strategic supply chain design . This gives us the opportunity to create holistic, global solutions that optimise the entire supply chain, including but not limited to what we do in the warehouse.
3PLs typically handle air freight, ocean freight, logistics and manufacturing, so we have a really good overview of the entire chain. Panalpina is very forward thinking when it comes to supply chain optimisation and we are committed to working with our customers to help them identify and remove waste.
What do you tend to notice about global supply chains when you apply VSM?
VSM gives us the chance to “zoom out” to see the problems we identified from a different perspective. That is when we sometimes realize that the original solution was not the best one. By applying value stream mapping we can to look at the complete system rather than individual points like a warehouse or a factory. We can look through the eyes of the stakeholders, the end customers and see the impact that our “solutions” would have on the other elements of the supply chain.
When we apply VSM to the entire supply chain we find that waste typically concentrates on the borders – at the handover points between suppliers and warehouses, warehouses and transport providers etc. Essentially at the intersection points where responsibility for the product changes hands.
But whilst it is important to remove waste, it’s also equally important to understand the impact of your actions on the whole ecosystem.
To give an example, a warehouse operator might want to improve their picking process, making picking faster, to get the product orders out on delivery as quickly as possible. But improving this one process without understanding the holistic view of the supply chain can create problems elsewhere. So if the warehouse operator starts picking orders quicker but the transportation provider is already operating at full capacity, then we will see a bottleneck start to accumulate. This means that the intended optimisation has actually decreased the efficiency of the supply chain by creating additional waste in overproduction.
Unfortunately, we see many companies that tend to focus on relatively minor issues when it comes to supply chain problems. We are using VSM to show them the full picture. How does each individual issue affect the whole? Which process has biggest impact on speed or efficiency? As with manufacturing, many supply chain activities end up in silos. It makes sense to understand the impact an improvement can have on the neighbouring process, to identify if with your solution you are just shifting the bottleneck.
So process improvement can be bad?
Sometimes! Of course it always depends, but value stream mapping really allows us to appreciate the butterfly effect in supply chains – change something at X, and there’s a massive impact at Y. Part of the issue is that certain parts of the supply chain are almost over-optimised. Manufacturing has become so lean and it is so easy to mass-produce cheap products that we are currently creating far more waste than ever before. The volume of products that are thrown away every year is immense. We consume far more product than we actually need.
Of course, it’s quite difficult to pinpoint the cause of this shift to a disposable attitude to products – are products becoming cheaper because consumer demand dictates that? Or is consumer demand simply growing due to the abundance of cheap products? It’s a bit of a chicken and egg scenario. My grandparents took care of everything they bought, if something got broken then they fixed it. But in today’s society we are so efficient at mass production that we can just throw old products away and buy something new.
We have never had so much waste in global supply chains and value stream mapping really helps us to understand why that is and where the waste is coming from. We can use this to focus energy on the vital activities that will really drive change and, quite often, these activities come as a big surprise. The waste often isn’t where you think it is.
Could VSM be further improved to generate even more value?
I think one area that is still underdeveloped is in the reverse loop – so with products that are coming back in to the supply chain after they have been purchased. Products that need to be repaired or recycled are very difficult to track and many companies are not paying much attention to reverse logistics, but if we had this information available during VSM then we really would have total visibility on products from start to finish.
There is an enormous market for returns and used items, from electronics to clothing, but many manufacturers don’t want to deal with the headache that reverse loop supply chains can generate. This is a shame, because we find that vast amounts of time, materials and money could be recouped by extending product lifecycles and ensuring that reusable products don’t end up in landfill.
What happens in a VSM workshop?
Our workshops run for one week and we work together with a cross-functional team that represents many different aspects of the customer’s business. We always recommend a holistic view, so the workshop generates the best results if we can really look at the entire supply chain. We bring in experts from each different area of the supply chain to track the entire movement of both physical goods and information. This builds a map that illuminates the entire supply chain, from which we can simulate the full product journey.
Value stream mapping allows us to visualise and identify problems; from then on we can use additional tools to fix issues and find the root cause. It is a great first step that we use to focus our energy and get to the heart of what’s going on in a supply chain.
And you can organise workshops for any company?
Yes, absolutely. Any customer with a complex supply chain would certainly benefit from value stream mapping. Panalpina is ready and willing to work together with existing or new customers to bring the benefits of a lean approach to their supply chains.
Maria Pia Caraccia was interviewed by Katy Huckle (December 2018).
For more information, contact mariapia.caraccia@panalpina.com
- Disruptions to Global Supply Chains, Sustainability, and the Inventory Time Bomb
- Sustainability is Driving New Business Dynamics – Repurposing and Connected Collaboration Across Supply Chains
- Digital Technologies – Poison and Medicine for ReMakers
- RemakerSpace reshapes the future
- If they haven’t already, the coronavirus will force companies to re-think their elongated supply chain.