Finding the weakest supply chain link
15 November 2018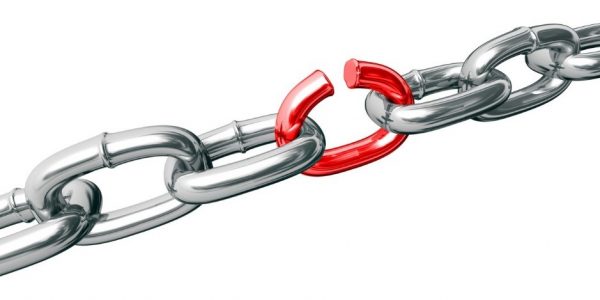
Blog post authors: Professor Mike Wilson (PARC Director) & Katy Huckle (PARC Co-ordinator)
PARC Insight: Should we be applying Lean principles to logistics? This PARC Insight takes a quick look at the time wasted on storing goods.
LEAN’S IN
Every woman and her dog has come across lean manufacturing by now, at least in its most basic format; be it six sigma training, a kaizen workshop, and other methods of hunting out Muda, or the 7 deadly wastes in lean manufacturing (if you don’t speak Japanese).
So what’s it all about? The premise that led to all those lean workshops, The Machine That Changed The World, The Toyota Production System; you name it – it all comes down to the elimination of waste. The Muda, or the non-value added activity, are generally accepted as overproduction, inventory, waiting, motion, transportation, rework and over-processing.
SUPPLY CHAIN MUDAS
Two important elements of Muda in this list are inventory and transportation, and yet we see supply chains built on the fundamentals of storing products as inventory and then transporting them to the point of consumption. Are these wasted efforts?
Across the globe, manufacturers have spent billions in improving their manufacturing efficiency to cut every bit of waste out of their processes. Single Minute Exchange of Dies, Poka Yoke, Kanban – all are designed to shave lead times, throughput times, and eliminate labour costs to make manufacturing more efficient. Engineers rack their brains for months on end to figure out how to reduce production lead times by a matter of seconds, take cents out of manufacturing costs, or even re-engineer products to make manufacturing more economical.
But all this happens INSIDE the factory. What happens when these products get out in to the world? They get stuck in slow, inefficient and unsustainable supply chains.
Why bother with all this optimisation when the end product can take days, weeks or even months to get to market.
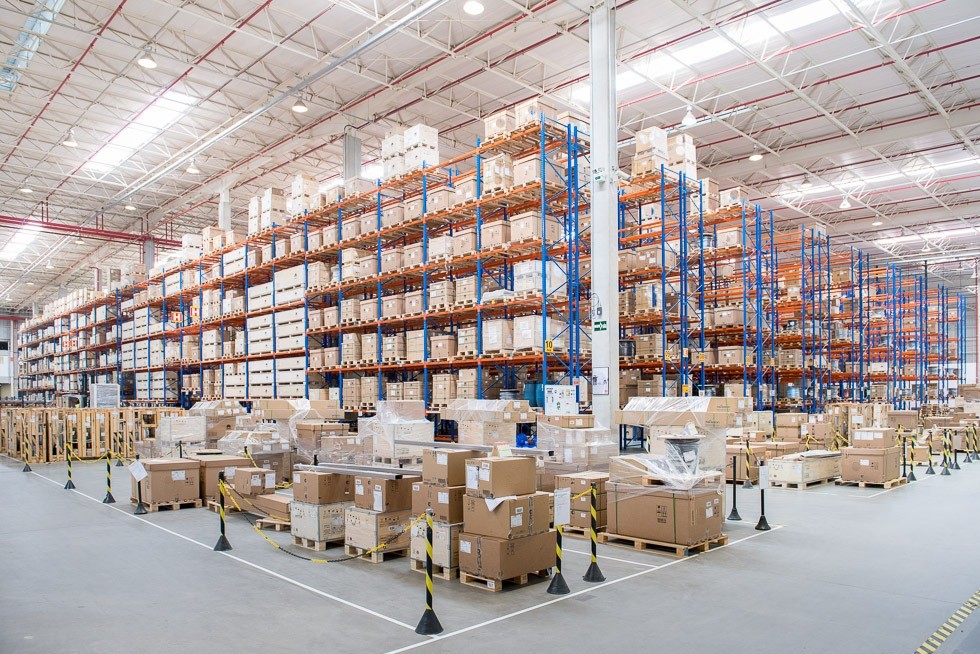
The basic principle of Goldratt’s Optimised Production Technology, or the Theory of Constraints, was to get the product out of the factory as soon as possible once it had passed the critical bottleneck operation. We know that the point of maximum product value is achieved when a finished good is ready for sale, which happens as soon as it exits the production line. Everything that happens to the product from that moment on is just a cost. So, shouldn’t we be applying lean thinking and philosophies to the entire supply chain?
Now, this is not to say that some transportation isn’t necessary, as product still has to get to market, but with the focus on speed to market and asset velocity, organisations are looking to cut the waste out of supply chains. Long distance product transportation is coming under more scrutiny as we look to reduce lead times and recognise that, using new technologies such as digital manufacturing, we could be adding value to the product as late as possible in the supply chain and then getting it to the customer as quickly as possible. This would increase speed to market, improve asset velocity, and minimize waste.
More and more companies are recognizing the need to get product to market faster than ever without increasing inventory levels. To achieve this goal, they need to rethink their mature, elongated (and wasteful) supply chains. As a general trend, we are starting to see supply chain decoupling; moving the value-adding processes closer to consumption. This behaviour can be wrapped up as the shift to near-shoring or re-shoring or distributed manufacturing, but the core of it is simple; apply the lean principles of waste elimination to supply chains and you will end up with something efficient, customer-focused and sustainable. We might just then be able to vindicate all that effort from the production teams in cutting out those extra, critical seconds.
- Disruptions to Global Supply Chains, Sustainability, and the Inventory Time Bomb
- Sustainability is Driving New Business Dynamics – Repurposing and Connected Collaboration Across Supply Chains
- Digital Technologies – Poison and Medicine for ReMakers
- RemakerSpace reshapes the future
- If they haven’t already, the coronavirus will force companies to re-think their elongated supply chain.